ELECTRONIC DOSING UNIT EDC
- Pneumatic drive: min. compressed air = 4 bar
- Feed speed: max. = 35 mm³ / stroke
- Max. frequency = 3 Hz / 180 strokes / min
The electronic dosing centre is used for all lubrication applications and is specially designed to handle various viscosities. In addition to conventional lubricants, other liquid fluids can also be processed, provided they can be used for the electronic dispensing centre and have been approved by WERUCON!
The device functions as a filling station, which can be equipped with different dosing nozzles. Originally, the medium is dosed without contact with the component using spray nozzles by adding spray air. The dispensing device can also be used as a supply station for contact lubrication (e.g., a lubricator for roller conveyors or similar), i.e. without spray air.
The device is used, for example, for the lubrication of sheet metal strips/dies on automatic punching presses. Contact and non-contact lubrication are possible in open or closed spray applications to wet from above and below. Point lubrication in the tool and safe lubrication for the tapping process are also possible.
The device is particularly advantageous when a flow rate proportional to the process must be continuously adjusted during operation or where individual nozzles must be selectively switched on or off.
MOD. EDC
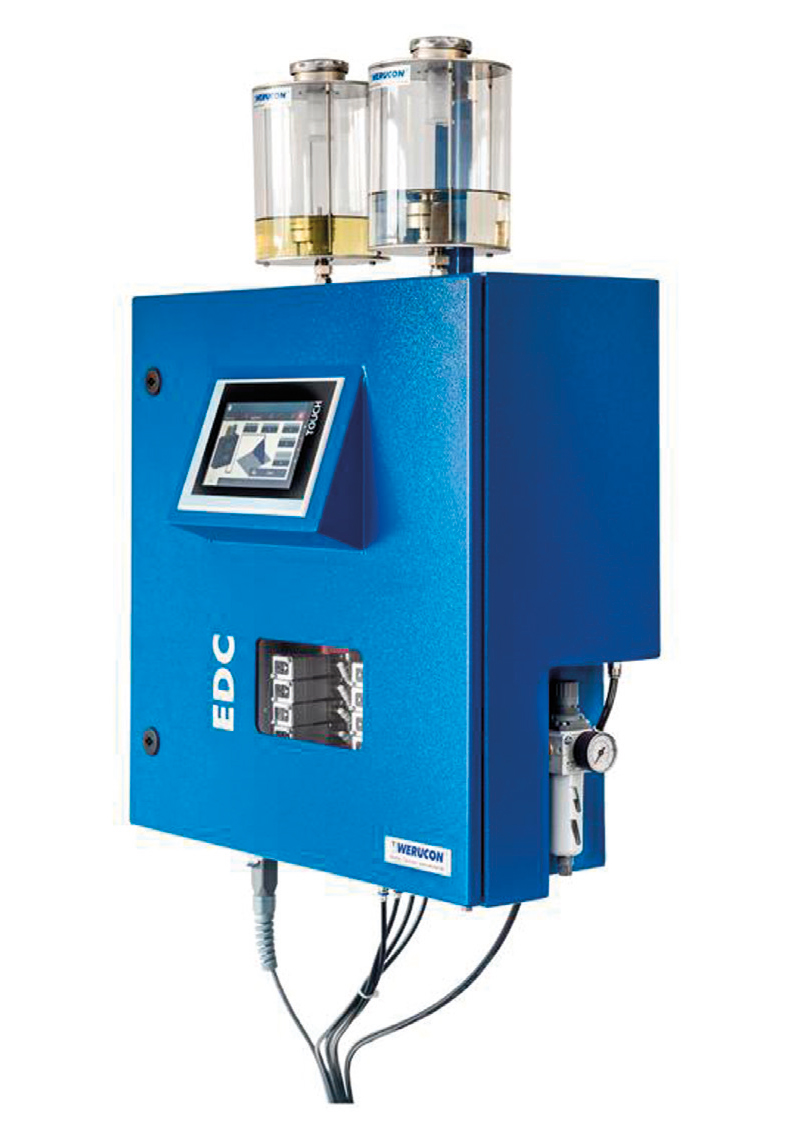